New research launched to make plastics circular
How do we ensure that plastic packaging materials can be reused? Or how can dyes in PET bottles be reused and contribute to the effort to make plastics circular? These and more research proposals were awarded in the call Making Plastics Circular: Technical Innovations. Maastricht University received grants for three of the ten research projects starting in the National Growth Fund program Circular Plastics NL.
Currently in the Netherlands, fifteen percent of the one million tons of plastics discarded in the Netherlands each year are recycled at high quality. The goal is for fifty percent of all plastics to be recycled by 2030 and production to be fully circular by 2050. What technical innovations can we use to ensure that plastics are reused more often? That is investigated in Making Plastics Circular: Technical Innovations.
There is six million euros divided among ten projects. All studies will last five years and fit within one of the following three themes:
- design of circular plastics;
- new characterisation, sorting and waste techniques;
- new recycling techniques.
Assigned projects Maastricht University
Top-down covalent adaptable and circular epoxy networks
Dr. K.V. Bernaerts (Maastricht University)
The European Green Deal promotes a shift towards a circular economy by 2050, and challenges polymer science to revolutionize the recycling of crosslinked materials. This project is pioneering an entirely new approach to making widespread epoxy-amine networks (e.g., wind turbine blades) recyclable. The key is a transformation of a bond present in the network to another bond so called reversible behavior under the influence of a stimulus (e.g., temperature), which enables recycling. This breakthrough in the recycling of epoxy-amine networks, will be validated on coatings and composites.
Consortium: Maastricht University, Westlake Epoxy
About the National Growth Fund Program Circular Plastics NL (CPNL)
The call Making Plastics Circular: Technical Innovations is part of the National Growth Fund Program Circular Plastics NL. By 2030, the Netherlands wants 50 percent of all plastics to be recycled and by 2050 there should be a fully circular plastics chain. The CPNL program runs for eight years and has eight program lines that focus on bottlenecks to close the cycles for existing plastics, provide sustainable growth opportunities for the Dutch economy and use grants to accelerate the transition.
About the National Growth Fund
Through the National Growth Fund (NGF), the government is investing 20 billion euros from 2021 to 2025 in projects that ensure long-term economic growth. Among other things, the National Growth Fund invests in research, development and innovation projects. In a number of these projects NWO is involved as one of the implementing organizations, including for organizing grant programs for scientific research or scientific talent.
Sustainable and fire-safe plastics based on fully organic phosphorus-sulfur compounds (SuFiP-S).
Dr. A. Gooneie (Maastricht University)
Polypropylene (PP) is an important base material for flame retardant products in the electronics and transportation industries. Single-molecule flame retardants (FR) such as phosphorus-sulfur (P-S) FRs represent one of the most advanced systems for PP due to their promising FR behavior at low concentrations. However, these systems are not yet commercially applied because the decomposition mechanisms are not sufficiently known during the processing phase and final application, leading to limited recyclability. This project embraces a systematic, interdisciplinary approach to the degradation, processing and recycling of PP/FR plastics to provide a scientific basis for developing new PP/FR materials and increasing the quantity and quality of recyclate.
Consortium: SABIC, Maastricht University
CLEANpack: Towards food safe Closed Loop rEcycling of pAckagiNg
Prof. Dr. Ir. S. de Meester (Maastricht University)
The goal of the CLEANpack project is to systematically analyze and improve advanced mechanical recycling technologies (or in a broader sense physical recycling processes) for closed-loop recycling of polyolefin-based food packaging. The project will provide an objective and unique scientific understanding of the potential of the most common advanced mechanical recycling options to achieve food-grade polyolefin recyclate. This work can then be used to guide policy and also investment in these technologies.
Consortium: Basell Polyolefin, BASF Chemetall, Danone S.A., The Kraft Heinz Company, Maastricht University, Ghent Universitystricht, Universiteit Gent
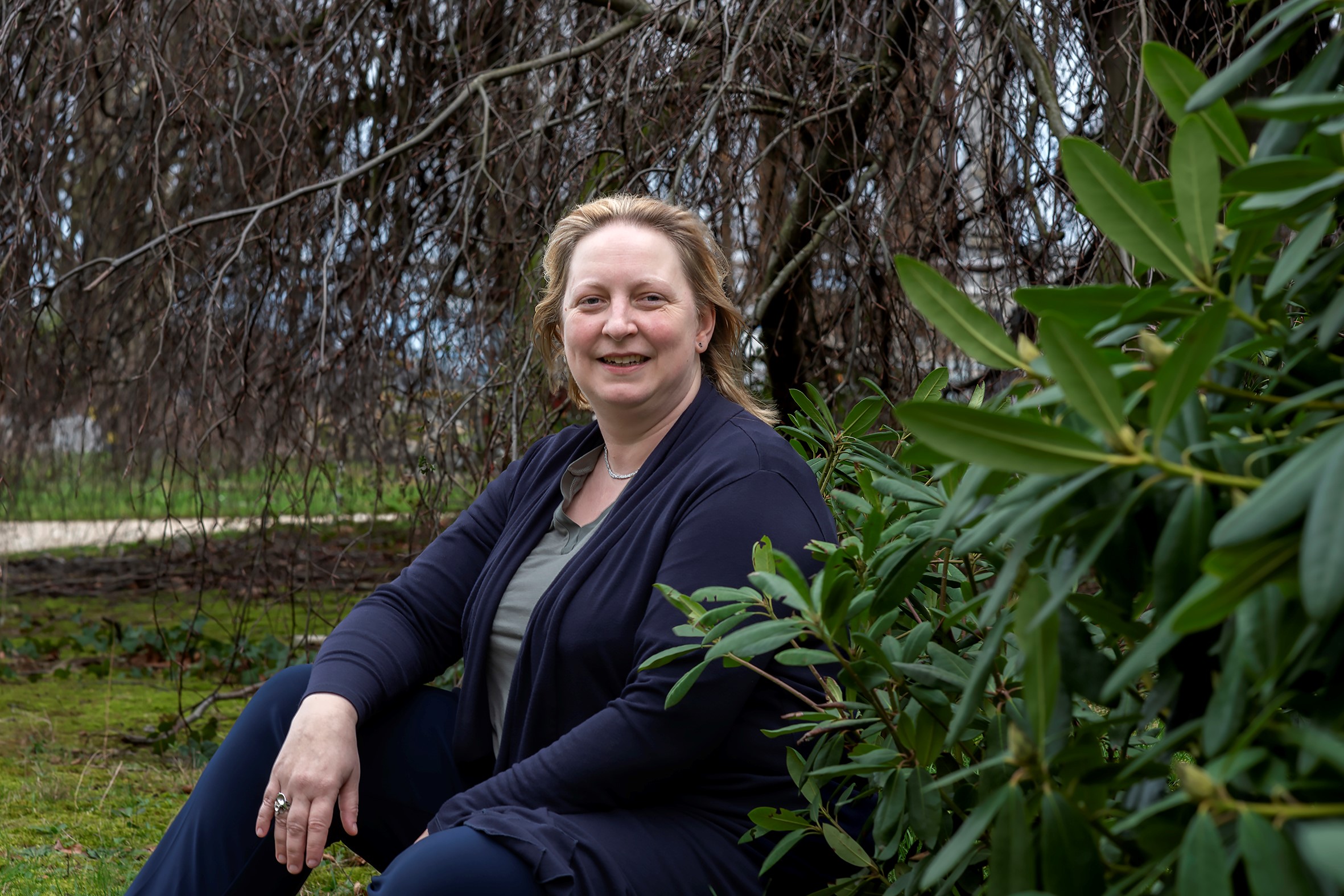
The Circular Plastics research group
Kim Ragaert founded the Circular Plastics research group three years ago, when she moved to Maastricht. Her work has laid the foundations for many innovations in the field of plastic recycling, and she is currently developing a research facility that will bring the plastic recycling world together.
Read more about Kim and the research group in this interview.
(Photography: Ellen Oosterhof)
Also read
-
Over the next four years, four young researchers can start research into crop biotechnology and engineering, thanks to the collaboration between Radboud University and Maastricht University. The researchers will start work at the Brightlands Campus Greenport in Venlo, halfway between the two...
-
It is with great sadness that Maastricht University has learned of the death of Frans de Waal. Frans de Waal was the first holder of the Eugène Dubois Chair at Maastricht University in 2015.
-
Intense exercise such as running can have an effect on your sense of taste and smell. Intensive sports are also known to have an effect on various processes in the body, all to keep our bodies balanced.